

a nyomtatott áramköri lapok (PCB-k) tesztelése a tervezési és gyártási folyamatok során elengedhetetlen a minőségi termékek biztosításához. Elkerüli azokat a helyzeteket, amikor a tervezők és a gyártók rájönnek, hogy a termék az utolsó pillanatban hibás, miközben a táblák teljes gyártásban vannak, vagy már a piacon vannak.
még a megfelelő tervezési és gyártási folyamatok követése után is mindig fennáll a hibák, hibák, emberi hibák kockázata a prototípus fázisaiban. E problémák azonosítása és kezelése a végtermék előtt kritikus fontosságú a termékek teljesítményének, funkcionalitásának és megbízhatóságának biztosítása szempontjából. A PCB-k hibáinak széles skálája merülhet fel emberi hiba, rossz gyártási folyamat, rossz tervezés és más gyakorlatok miatt.
a tesztelés előnyei közé tartozik a
- hibák és hibák azonosítása és kezelése, például rövidzárlat, nyitás, rossz forrasztás, funkcionális problémák stb.
- ez lehetőséget ad arra, hogy minden lehetséges problémát korai szakaszban kezeljen, mielőtt a végső gyártásba kerülne, időt és pénzt takarítva meg. A késztermékek problémáinak megoldása általában nehezebb, időigényes és költséges
- a pazarlás és a költségek csökkentése, mivel a tesztelők a kis méretű szerelvényeket és prototípusokat használják a teljes termékek helyett. Ez megakadályozza a hibás, teljes körű szerelvények eldobását.
a PCB több különböző részből és alkatrészből áll. Ezek mindegyike hatással van az áramkör teljes teljesítményére és az elektronikai egység egészére. Ideális esetben fontos mindent tesztelni. Ez magában foglalja, de nem kizárólagosan a;
- elektromos vezetőképesség
- mechanikai szilárdság
- forrasztás minősége
- tisztaság
- vizsgálatok a célkörnyezet
- laminálás — peel szilárdság
- minőségi lyuk fal
- alkatrész elhelyezése, igazítás, polaritás, tájolás stb.
PCB tesztelési technikák
általában a tesztelés magában foglalja a tervezési jellemzők ellenőrzését a vizuális, szerkezeti, elektromos és funkcionalitás szempontjából. A legtöbb esetben különböző technikák léteznek ezeknek a területeknek a tesztelésére, és a választás olyan tényezőktől függ, mint a tábla összetettsége, alkalmazása, tervezése stb. A közös módszerek a következők;
- in-circuit tesztelés (ICT)
- JTAG boundary-scan
- automatizált optikai ellenőrzés (AOI)
- automatizált röntgen vizsgálat (AXI)
a tesztelő csapatok kézi szemrevételezéssel (MVI) vagy automatizált tesztberendezéssel (ate) ellenőrizhetik a PCB-ket az összeszerelési folyamat után. Az automatikus vizsgálati módszerek, mint például az automatizált optikai ellenőrzés AOI) és az automatizált röntgenvizsgálat (AXI) hatékonyabbak az összeszerelési szintű vizsgálatokhoz, de általában költségesek.
az érintkezők vizuális és elektromos tesztjei mellett egyes alkalmazások, mint például a katonai, űrkutatási, Bányászati és hasonló iparágak mechanikai vizsgálatokat igényelnek. Ez biztosítja, hogy a BGA és más alkatrészek ellenálljanak az ütéseknek, rezgéseknek és más durva körülményeknek a működési környezetben. A legtöbb esetben a tesztek destruktívak, és magukban foglalják a PCB-t sokk-és nyíróerőknek. A törzs mérése segít meghatározni a forrasztási kötések mechanikai tulajdonságait.
in-circuit testing (ICT)
az ICT tartalmaz egy in-circuit tester, egy lámpatest, és a szoftver, és képes fedezni a legtöbb hibát, amelyek előfordulnak a gyártási folyamatok során. A tesztelők használhatják rövidnadrág, nyitás, ellenállás, kapacitás és induktivitás ellenőrzésére, valamint a diódák, tranzisztorok és IC-k polaritásának vagy tájolásának ellenőrzésére.
az áramköri tesztek a tervezési modell alapján ellenőrzik az alkatrészeket. Elméletileg a PCB-hibák körülbelül 98% – át képes felismerni. Ez azonban gyakorlatilag nem lehetséges, különösen akkor, ha nem tud hozzáférni az összes csomóponthoz, valamint képtelen mérni a nagyon alacsony kapacitás-és induktivitási értékeket.
az IKT előnyei közé tartozik az egyszerű hibakeresés, a programozás és a könnyen értelmezhető vizsgálati jelentések. Ennek azonban vannak hátrányai, például költséges berendezések, nehézségek a tesztberendezés-rendszerek frissítésében, mivel azok mechanikusan rögzítettek, képtelenség hozzáférni egyes csomópontokhoz összetett áramkörökben stb.
a két általánosan használt IKT-technika a körömágy és a repülő szonda. Mindegyiknek megvan a maga helye, előnyei és korlátai, és a választás a vizsgált PCB jellegétől és összetettségétől függ.
szögágy technika
a szögágy vagy az univerzális rács áramköri tesztelése több rugós pogo csapra támaszkodik, amelyek érintkeznek a NYÁK több pontjával. Ezek a csapok hasonlítanak a körömágyra, így a név. A teszt során a pogo csapok mindegyike érintkezik az áramkör csomópontjával vagy a vizsgált ponttal. Ez a módszer képes azonosítani, rövidnadrágot, nyitást, forrasztási hidakat, hibás alkatrészeket és egyéb PCB hibákat.
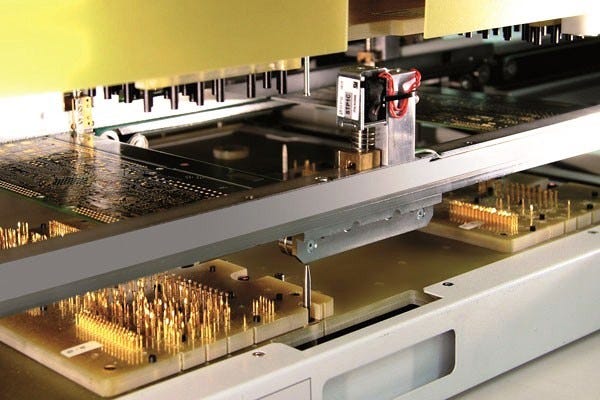
egy tipikus áramköri teszt több csapból áll, amelyek az egész táblán elterjedtek. A többszörös csapok alkalmazása több tíz vagy több száz egyidejű kapcsolatot és tesztet biztosít. Ezek mindegyike körülbelül 35 mm hosszú, és általában egy háló, például egy felületre szerelhető pad, egy lyuk vagy egy tesztpont végén helyezkednek el. Ha az összes hálót csatlakoztatják, a teszt körülbelül 7 másodpercet vesz igénybe.
a vizsgálat során a csapok bizonyos jeleket és feszültségeket vezetnek be az áramkörbe, majd a kapott értékeket lefelé mérik.
általában a körömágy technika egy gyors, olcsó vizsgálati módszer, amely alkalmas tömeggyártási rendszerekhez, egyszerű áramkörökhöz és analóg táblákhoz. Ez azonban korlátozott lehet, ha összetett táblákkal dolgozik, különösen azokkal, amelyek kis hangmagassággal, SMD-kkel, BGA-val és hasonló alkatrészekkel rendelkeznek.
repülő szonda teszt
a technika egy kisebb hangmagasságú elemet használ a vizsgálati pontokkal, például az SMD csapokkal való érintkezéshez. Ez alkalmas kis méretű érintkezőkhöz 0,2 mm-es tesztmagasságig. A gyakorlatban több szondát használ, hogy érintkezzen a csapokkal, párnákkal és viákkal, és tesztelje a nyitásokat, a rövidnadrágokat és az elektromos paramétereket, például a polaritást, az ellenállást és a kapacitást.
egyes tesztberendezések tartalmazhatnak kamerát annak megállapítására, hogy vannak-e hiányzó alkatrészek, és elemezhetik az alkatrészek méretét, alakját, tájolását, polaritását és egyéb fizikai tulajdonságait.
automatizált optikai ellenőrzés (Aoi)
az AOI módszer egy vagy több kamerát használ a NYÁK optikai elemzéséhez. Szoftver segítségével összehasonlítja a vizsgált PCB képeit egy hasonló referenciatáblával. Egy másik lehetőség az ideális tervezési specifikációkkal való összehasonlítás. Az optikai ellenőrzés általában a futószalag végén található, ahol segít a késztermék minőségének ellenőrzésében.
az összeszerelés alatt álló PCB-n végzett tesztek kivételével az AOI módszer figyelemmel kísérheti a gyártási folyamatot. A pick and place gépekben alkalmazott technológia lehetővé teszi a gyártók számára, hogy valós időben nyomon kövessék a folyamatokat, és kijavítsák az összeszerelési hibákat, például az alkatrészek esetleges helytelen elhelyezését és az eltérést.

egyes alkalmazásokban az optikai ellenőrzés magában foglalja az endoszkóp használatát a BGA és a PCB közötti kapcsolatok megtekintéséhez.
az AOI módszer csak olyan PCB-Ken használható, ahol a vizsgálandó pontok optikailag láthatók.
automatizált röntgenvizsgálat (AXI)
az AXI roncsolásmentes vizsgálati technikát biztosít, amely képes az emberi szem számára láthatatlan forrasztási hibák kimutatására vagy az automatikus optikai ellenőrzés használatakor. Nem igényel fizikai kapcsolatot, és hibákat találhat a nagy IC csomagok alatt, mint például a BGA, Micro BGA, QFN, LGA, CSPs stb.

általában a röntgen technika alkalmas a központban található láthatatlan területek tesztelésére. A módszer azon alapul, hogy az anyagok képesek elnyelni a röntgensugarakat vastagságuk és atomszámuk szerint. Mivel az abszorpciós sebesség egyenesen arányos az elem atomtömegével, a nehezebb anyagok, mint például a forraszanyag, általában több röntgensugarat vesznek fel, és jobban láthatóak. A könnyebb elemek, például az integrált áramkör csomag átlátszóbbnak tűnnek, mivel kevesebb röntgensugarat vesznek fel.
a BGA tipikus röntgenképe az alábbiakban látható. A viszonylag átlátszó szakaszok könnyebb anyagokra utalnak, míg a sötétebb részek a nehezebb részeket, például a forrasztást tükrözik.
mint ilyen, a röntgensugarak behatolhatnak az IC csomagba, és megvizsgálhatják a forrasztást és a csatlakozásokat, ahol olyan szerkezeti hibákat azonosítanak, mint a rövidnadrág, a nyílások, az elégtelen forrasztás, a felesleges forrasztás és az ürítés.
egyéb képességek közé ellenőrzése
- rossz igazítás a BGA és más nagy chipek
- kapcsolatok, amelyek nem szimmetrikus
- összhang a csomag standoff magasság
- Popcorning — ami akkor következik be, amikor néhány golyó összeolvad alkotnak szabálytalan alakzatok
- forrasztás elemzés, ahol ellenőrzi a belső a forrasztási hibák, például buborékok, elégtelen töltés stb.
a módszer ideális a tábla, a rétegek, a forrasztás, az alkatrész tájolása, igazítása és egyéb fizikai jellemzők ellenőrzésére.
PCB tesztelési megoldás kiválasztása
a technikák a PCB típusától, az elvégzendő teszteléstől, az alkalmazástól, az érzékenységtől és a toleranciától függően változnak. Például az orvosi, űrkutatási, katonai és hasonló alkalmazások magasabb szintű megbízhatóságot igényelnek.
leggyakrabban könnyű ellenőrizni egy egyszerű, egy-vagy kétrétegű PCB-t hagyományos vizsgálati módszerekkel. Mivel azonban a komplexitás szintje növekszik a nagy komponenssűrűség, a több réteg, a miniatürizálás és más tényezők miatt, a tesztelés olyan fejlett technikákat igényel, mint az Aoi és az AXI.
az áramkörön belüli tesztelés a legtöbb alapvető áramkörnél működni fog, de a komplexitás és az alkatrészsűrűség növekedésével más technikák, például az Aoi és az AXI szükségessé válnak. A röntgensugár alkalmas nagy chipekkel rendelkező PCB-khez, például a BGA – khoz és másokhoz, ahol egyes csatlakozások még optikai módszer használata esetén is láthatatlanok.