

La prueba de placas de circuito impreso (PCB) en todos los procesos de diseño y fabricación es esencial para garantizar productos de calidad. Evita situaciones en las que los diseñadores y fabricantes se dan cuenta de que el producto es defectuoso en el último minuto, mientras las tablas están en plena producción o ya están en el mercado.
Incluso después de seguir los procesos de diseño y fabricación adecuados, siempre hay un riesgo de defectos, errores, errores humanos en las etapas del prototipo. Identificar y abordar estos problemas antes del producto final es fundamental para garantizar el rendimiento, la funcionalidad y la fiabilidad de los productos. Una amplia gama de defectos en los PCB pueden surgir debido a errores humanos, un proceso de fabricación incorrecto, un diseño deficiente y otras prácticas.
Los beneficios de las pruebas incluyen
- Identificar y abordar fallas y errores como cortocircuitos, aperturas, soldadura deficiente, problemas funcionales y más.
- Brinda la oportunidad de abordar cualquier problema potencial antes de comenzar la producción final, ahorrando tiempo y dinero. Solucionar los problemas en los productos terminados suele ser más difícil, lento y costoso
- Reducir el desperdicio y los costos, ya que los probadores utilizan los conjuntos y prototipos a pequeña escala en lugar de productos completos. Esto evita que se desechen los ensamblajes defectuosos a gran escala.
Una PCB consta de varias piezas y componentes diferentes. Cada uno de ellos tiene un impacto en el rendimiento general del circuito y el conjunto de la electrónica en su conjunto. Idealmente, es importante probar todo. Esto incluye, pero no se limita a verificar el;
- Conductividad eléctrica
- Resistencia mecánica
- Calidad de soldadura
- Limpieza
- Pruebas para el entorno objetivo
- Resistencia a la laminación y al pelado
- Calidad de la pared del orificio
- Colocación de componentes, alineación, polaridad, orientación, etc.
Técnicas de prueba de PCB
En general, las pruebas implican verificar las características de diseño en términos visuales, estructurales, eléctricos y funcionales. En la mayoría de los casos, hay varias técnicas para probar cada una de estas áreas, y la elección depende de factores como la complejidad de la placa, la aplicación, el diseño, etc. Los métodos comunes incluyen;
- Pruebas en circuito (ICT)
- Exploración de límites JTAG
- Inspección óptica automatizada (AOI)
- Inspección por rayos X automatizada (AXI)
Los equipos de prueba pueden usar métodos de inspección visual manual (MVI) o equipos de prueba automatizados (ATE) para verificar los PCB después del proceso de ensamblaje. Sin embargo, los métodos de prueba automáticos, como la Inspección Óptica Automatizada AOI) y la Inspección por Rayos X Automatizada (AXI) son más eficaces para las pruebas de nivel de montaje, pero generalmente son costosos.
Además de las pruebas visuales y eléctricas en los contactos, algunas aplicaciones como las industrias militar, aeroespacial, minera y similares requieren pruebas mecánicas. Esto garantiza que el BGA y otros componentes resistan los golpes, las vibraciones y otras condiciones difíciles en los entornos operativos. En la mayoría de los casos, las pruebas son destructivas e implican someter la PCB a fuerzas de choque y cizallamiento. La medición de la tensión ayuda a establecer las propiedades mecánicas de las juntas de soldadura.
Prueba en circuito (ICT)
La ICT comprende un comprobador en circuito, un accesorio y el software y puede cubrir la mayoría de los defectos que ocurren durante los procesos de fabricación. Los probadores pueden usarlo para verificar si hay cortocircuitos, aperturas, resistencia, capacitancia e inductancia, además de verificar la polaridad u orientación para dispositivos como diodos, transistores e circuitos integrados.
Las pruebas en circuito comprueban los componentes basándose en un modelo del diseño. Teóricamente, tiene el potencial de detectar aproximadamente el 98% de las fallas de PCB. Sin embargo, esto puede no ser prácticamente posible, especialmente cuando no puede acceder a todos los nodos, así como su incapacidad para medir valores de capacitancia e inductancia muy bajos.
Los beneficios de las TIC incluyen detección de defectos sencilla, programación e informes de prueba fáciles de interpretar. Sin embargo, tiene inconvenientes, como equipos costosos, dificultades para actualizar los sistemas de los equipos de prueba, ya que se fijan mecánicamente, imposibilidad de acceder a algunos nodos en circuitos complejos, etc.
Las dos técnicas TIC comúnmente utilizadas son la Cama de clavos y la sonda voladora. Cada uno tiene su lugar, beneficios y limitaciones, y la elección depende de la naturaleza y complejidad de la PCB bajo prueba.
Técnica de lecho de clavos
El lecho de clavos o la prueba en circuito de rejilla universal se basa en múltiples pasadores pogo con resorte que hacen contacto con varios puntos en la PCB. Estos alfileres se asemejan a la cama de clavos, de ahí el nombre. En la prueba, cada uno de los pines pogo hace contacto con el nodo del circuito o el punto bajo prueba. Este método puede identificar, cortocircuitos, aperturas, puentes de unión de soldadura, componentes defectuosos y otras fallas de PCB.
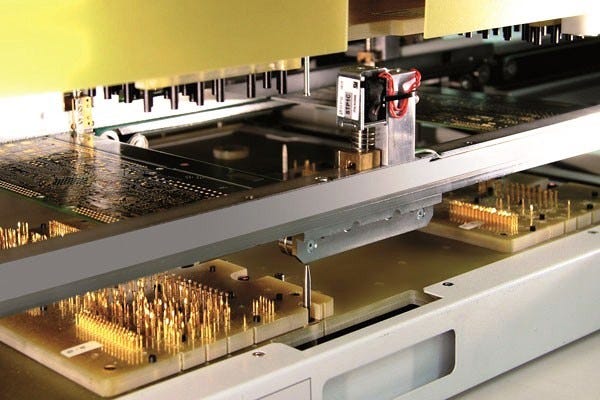
Una prueba típica en circuito se compone de múltiples pines repartidos por el tablero. La aplicación de los múltiples pines garantiza decenas o cientos de conexiones y pruebas simultáneas. Cada uno de ellos mide aproximadamente 35 mm de largo y generalmente se inserta en el extremo de una red, como una almohadilla de montaje en superficie, un orificio o un punto de prueba. Con todas las redes conectadas, la prueba tarda unos 7 segundos.
Durante la prueba, los pines introducen algunas señales y tensiones en el circuito después de lo cual miden los valores resultantes en la línea.
Generalmente, la técnica de cama de clavos es un método de prueba rápido y de bajo costo que es adecuado para sistemas de producción en masa, circuitos simples y placas analógicas. Sin embargo, puede ser limitado cuando se trabaja con placas complejas y especialmente con anchos de paso pequeños, SMD, BGA y componentes similares.
Prueba de sonda voladora
La técnica utiliza un elemento con un paso más pequeño para hacer contacto con los puntos de prueba, como los pines SMD. Esto es adecuado para contactos pequeños de hasta 0,2 mm de paso de prueba. En la práctica, utiliza varias sondas para hacer contacto con los pines, almohadillas y vías y probar aperturas, cortocircuitos y parámetros eléctricos como la polaridad, la resistencia y la capacitancia.
Algunos equipos de prueba pueden incluir una cámara para determinar si faltan componentes y analizar los tamaños, formas, orientación, polaridad y otras propiedades físicas de los componentes.
Inspección Óptica automatizada (AOI)
El método AOI utiliza una o varias cámaras para analizar ópticamente la PCB. Utiliza software para comparar las imágenes de la PCB bajo prueba con las de una placa de referencia similar. Otra opción es comparar con las especificaciones de diseño ideales. La inspección óptica suele realizarse al final de la línea de montaje, donde ayuda a verificar la calidad del producto terminado.
Aparte de realizar pruebas en la PCB bajo ensamblaje, el método AOI puede monitorear el proceso de fabricación. El uso de la tecnología en las máquinas de pick and place permite a los fabricantes rastrear los procesos en tiempo real y corregir defectos de montaje, como la posible extravío y desalineación de los componentes.

En algunas aplicaciones, la inspección óptica implica el uso de un endoscopio para ver las conexiones entre el BGA y la PCB.
El método AOI solo es útil en PCB en los que los puntos a probar son ópticamente visibles.
Inspección de rayos X automatizada (AXI)
AXI proporciona una técnica de prueba no destructiva con la capacidad de detectar defectos de soldadura invisibles para el ojo humano o cuando se utiliza la inspección óptica automática. No requiere una conexión física y puede encontrar defectos en los paquetes de circuitos integrados grandes, como BGA, Micro BGAs, QFN, LGA, CSP, etc.

En general, la técnica de rayos X es adecuada para probar áreas invisibles ubicadas en el centro. El método se basa en la capacidad de los materiales para absorber los rayos X de acuerdo con su grosor y número atómico. Debido a que la tasa de absorción es directamente proporcional al peso atómico del elemento, los materiales más pesados, como la soldadura, generalmente absorben más rayos X y son más visibles. Los elementos más ligeros, como el paquete de circuitos integrados, parecen más transparentes porque absorben menos rayos X.
Una imagen de rayos X típica de un BGA es la que se muestra a continuación. Las secciones relativamente transparentes se refieren a materiales más ligeros, mientras que las partes más oscuras reflejan partes más pesadas, como la soldadura.
Como tal, los rayos X pueden penetrar el paquete IC e inspeccionar la soldadura y las conexiones donde identifica defectos estructurales como cortocircuitos, aperturas, soldadura insuficiente, soldadura en exceso y vaciado.
Otras capacidades incluyen la comprobación de
- Mala alineación para el BGA y otros chips grandes
- Conexiones que no son simétricas
- Consistencia de la altura de separación del paquete
- interior de la soldadura para identificar defectos como burbujas, relleno insuficiente, etc.
El método es ideal para comprobar la placa, sus capas, soldadura, orientación de los componentes, alineación y otras características físicas.
Elegir una solución de prueba de PCB
Las técnicas varían según el tipo de PCB, las pruebas a realizar, la aplicación, la sensibilidad y la tolerancia. Por ejemplo, las aplicaciones médicas, aeroespaciales, militares y similares requieren mayores niveles de fiabilidad.
La mayoría de las veces, es fácil verificar una PCB simple, de una o dos capas utilizando métodos de prueba tradicionales. Sin embargo, a medida que aumenta el nivel de complejidad debido a altas densidades de componentes, múltiples capas, miniaturización y otros factores, las pruebas requieren técnicas avanzadas como AOI y AXI.
Las pruebas en circuito funcionarán para la mayoría de los circuitos básicos, pero a medida que aumenta el nivel de complejidad y la densidad de los componentes, se hacen necesarias otras técnicas como AOI y AXI. Los rayos X son adecuados para PCB con chips grandes como los BGA y otros donde algunas conexiones son invisibles incluso cuando se usa el método óptico.