

Test di schede a circuito stampato (Pcb) durante i processi di progettazione e produzione è essenziale per garantire prodotti di qualità. Evita situazioni in cui progettisti e produttori si rendono conto che il prodotto è difettoso all’ultimo minuto, mentre le schede sono in piena produzione o già sul mercato.
Anche dopo aver seguito corretti processi di progettazione e produzione, c’è sempre il rischio di difetti, bug, errori umani nelle fasi di prototipo. Identificare e affrontare questi problemi prima del prodotto finale è fondamentale per garantire le prestazioni, la funzionalità e l’affidabilità dei prodotti. Una vasta gamma di difetti nei PCB può sorgere a causa di errore umano, un processo di fabbricazione sbagliato, design scadente e altre pratiche.
I vantaggi del test includono
- Identificazione e risoluzione di errori e bug come cortocircuiti, aperture, scarsa saldatura, problemi funzionali e altro ancora.
- Offre l’opportunità di affrontare eventuali potenziali problemi prima di entrare nella produzione finale, risparmiando tempo e denaro. Risolvere i problemi sui prodotti finiti è di solito più difficile, dispendioso in termini di tempo e costoso
- Ridurre gli sprechi e i costi poiché i tester utilizzano assemblaggi e prototipi su piccola scala invece di prodotti completi. Ciò impedisce di gettare via assemblaggi difettosi e su larga scala.
Un PCB è costituito da diverse parti e componenti. Ognuno di questi ha un impatto sulle prestazioni complessive del circuito e del gruppo elettronico nel suo complesso. Idealmente, è importante testare tutto. Ciò include, a titolo esemplificativo ma non esaustivo, la verifica;
- conducibilità Elettrica
- resistenza Meccanica
- Saldatura di qualità
- Pulizia
- Test per l’ambiente di destinazione
- Laminazione — buccia di forza
- Qualità di foro muro
- posizionamento dei Componenti, l’allineamento, la polarità, orientamento, etc.
Tecniche di prova del PWB
Generalmente, la prova comprende la verifica delle caratteristiche di progettazione in termini di visivo, strutturale, elettrico e di funzionalità. Nella maggior parte dei casi, esistono varie tecniche per testare ciascuna di queste aree e la scelta dipende da fattori quali complessità della scheda, applicazione, progettazione, ecc. I metodi comuni includono;
- Test in-circuit (ICT)
- JTAG boundary-scan
- Automated optical inspection (AOI)
- Automated X-ray inspection (AXI)
I team di test possono utilizzare metodi di ispezione visiva manuale (MVI) o di apparecchiature di prova automatizzate (ATE) per controllare i PCB dopo il processo di assemblaggio. Tuttavia, i metodi di prova automatici, quali l’ispezione ottica automatizzata AOI) e l’ispezione automatizzata dei raggi X (AXI) sono più efficaci per le prove livellate dell’assemblea, ma solitamente costose.
Oltre ai test visivi ed elettrici sui contatti, alcune applicazioni come le industrie militari, aerospaziali, minerarie e simili richiedono test meccanici. Questo assicura che il BGA e altri componenti in grado di sopportare gli urti, vibrazioni e altre condizioni di massima in ambienti operativi. Nella maggior parte dei casi, i test sono distruttivi e comportano il sottoporre il PCB a forze di shock e taglio. Misurare lo sforzo aiuta a stabilire le proprietà meccaniche dei giunti di saldatura.
Test in-circuit (ICT)
L’ICT comprende un tester in-circuit, un apparecchio e il software e può coprire la maggior parte dei difetti che si verificano durante i processi di produzione. I tester possono usarlo per verificare la presenza di pantaloncini, aperture, resistenza, capacità e induttanza, oltre a verificare la polarità o l’orientamento per dispositivi come diodi, transistor e circuiti integrati.
I test in-circuit controllano i componenti sulla base di un modello del progetto. Teoricamente, ha il potenziale per rilevare circa il 98% dei guasti PCB. Tuttavia, questo potrebbe non essere praticamente possibile, specialmente quando non può accedere a tutti i nodi, così come la sua incapacità di misurare valori di capacità e induttanza molto bassi.
I vantaggi delle TIC includono la semplice rilevazione dei difetti, la programmazione e la facile interpretazione dei rapporti di prova. Tuttavia, presenta inconvenienti come attrezzature costose, difficoltà nell’aggiornamento dei sistemi delle apparecchiature di prova poiché sono fissati meccanicamente, incapacità di accedere ad alcuni nodi in circuiti complessi, ecc.
Le due tecniche ICT comunemente utilizzate sono il letto di chiodi e la sonda volante. Ognuno ha il suo posto, i suoi benefici e i suoi limiti e la scelta dipende dalla natura e dalla complessità del PCB in prova.
Tecnica del letto di chiodi
Il letto di chiodi o il test in-circuit della griglia universale si basa su più pin pogo caricati a molla che entrano in contatto con diversi punti sul PCB. Questi perni assomigliano al letto delle unghie, da cui il nome. Nella prova, ciascuno dei perni di pogo fa un contatto con il nodo del circuito o il punto nell’ambito della prova. Questo metodo può identificare, pantaloncini, si apre, ponti di saldatura, componenti difettosi e altri difetti PCB.
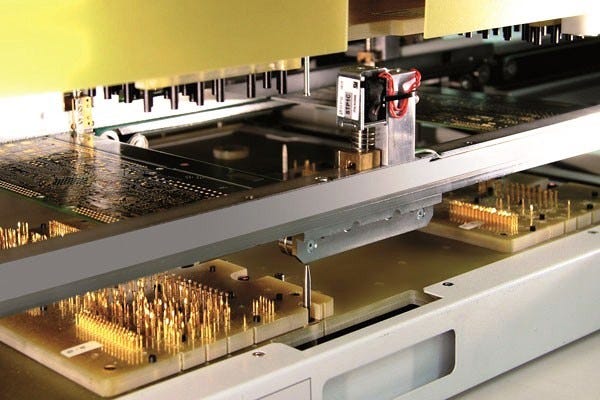
Un tipico test in-circuit comprende più pin sparsi su tutta la linea. L’applicazione dei pin multipli garantisce decine o centinaia di connessioni e test simultanei. Ognuno di questi è lungo circa 35 mm e solitamente inserito all’estremità di una rete come un pad di montaggio superficiale, un foro o un punto di prova. Con tutte le reti collegate, il test dura circa 7 secondi.
Durante il test, i pin introducono alcuni segnali e tensioni nel circuito dopo di che misurano i valori risultanti lungo la linea.
Generalmente, la tecnica bed of nails è un metodo di prova veloce e a basso costo adatto per sistemi di produzione di massa, circuiti semplici e schede analogiche. Tuttavia, può essere limitato quando si lavora con schede complesse e in particolare quelle con larghezze di passo ridotte, SMDS, BGA e componenti simili.
Flying probe test
La tecnica utilizza un elemento con un passo più piccolo per entrare in contatto con i punti di prova come i perni SMD. Questo è adatto per contatti di piccole dimensioni fino a un passo di prova di 0,2 mm. In pratica, utilizza diverse sonde per entrare in contatto con pin, pad e vias e testare aperture, pantaloncini e parametri elettrici come la polarità, la resistenza e la capacità.
Alcune apparecchiature di prova possono includere una telecamera per determinare se mancano componenti e analizzare le dimensioni, le forme, l’orientamento, la polarità e altre proprietà fisiche dei componenti.
Automated Optical Inspection (AOI)
Il metodo AOI utilizza una o più telecamere per analizzare otticamente il PCB. Utilizza un software per confrontare le immagini del PCB in prova con quelle di una scheda di riferimento simile. Un’altra opzione è quella di confrontare con le specifiche di design ideali. L’ispezione ottica è solitamente alla fine della catena di montaggio dove aiuta a verificare la qualità del prodotto finito.
Oltre a eseguire test sul PCB sotto assemblaggio, il metodo AOI può monitorare il processo di produzione. L’utilizzo della tecnologia nelle macchine pick and place consente ai produttori di monitorare i processi in tempo reale e correggere i difetti di assemblaggio, come potenziali errori di posizionamento e disallineamento dei componenti.

In alcune applicazioni, l’ispezione ottica prevede l’utilizzo di un endoscopio per visualizzare le connessioni tra il BGA e il PCB.
Il metodo AOI è utile solo su PCB in cui i punti da testare sono otticamente visibili.
Automated X-ray inspection (AXI)
AXI fornisce una tecnica di prova non distruttiva con la capacità di rilevare difetti di saldatura invisibili all’occhio umano o quando si utilizza l’ispezione ottica automatica. Non richiede una connessione fisica e può trovare difetti sotto i grandi pacchetti IC come BGA, Micro BGA, QFN, LGAS, CSP, ecc.

Generalmente, la tecnica a raggi X è adatta per testare aree invisibili situate al centro. Il metodo si basa sulla capacità dei materiali di assorbire i raggi X in base al loro spessore e numero atomico. Poiché il tasso di assorbimento è direttamente proporzionale al peso atomico dell’elemento, i materiali più pesanti come la saldatura di solito assorbono più raggi X e sono più visibili. Gli elementi più leggeri come il pacchetto di circuiti integrati appaiono più trasparenti perché assorbono meno raggi X.
Una tipica immagine a raggi X di un BGA è come mostrato di seguito. Le sezioni relativamente trasparenti si riferiscono a materiali più leggeri mentre le parti più scure riflettono parti più pesanti come la saldatura.
Come tale, i raggi X possono penetrare il pacchetto IC e ispezionare la saldatura e le connessioni in cui identifica difetti strutturali come pantaloncini, si apre, saldatura insufficiente, saldatura in eccesso e svuotamento.
Altre funzionalità includono il controllo per
- Cattivo allineamento per il BGA e di altri grandi chip
- Connessioni che non sono simmetrici
- Consistenza del pacchetto situazione di stallo altezza
- Popcorning, che si verifica quando alcune palle che si fondono per formare forme irregolari
- Saldatura di analisi in cui si verifica all’interno della lega per saldatura per identificare difetti come bolle, insufficiente riempimento, etc.
Il metodo è ideale per controllare la scheda, i suoi strati, la saldatura, l’orientamento dei componenti, l’allineamento e altre caratteristiche fisiche.
Scelta di una soluzione di test PCB
Le tecniche variano in base al tipo di PCB, ai test da eseguire, all’applicazione, alla sensibilità e alla tolleranza. Ad esempio, le applicazioni mediche, aerospaziali, militari e simili richiedono livelli più elevati di affidabilità.
Molto spesso, è facile controllare un PCB semplice, singolo o a due strati utilizzando metodi di prova tradizionali. Tuttavia, poiché il livello di complessità aumenta a causa delle elevate densità dei componenti, dei livelli multipli, della miniaturizzazione e di altri fattori, i test richiedono tecniche avanzate come AOI e AXI.
I test in-circuit funzioneranno per la maggior parte dei circuiti di base, ma man mano che il livello di complessità e la densità dei componenti aumentano diventano necessarie altre tecniche come AOI e AXI. X-ray è adatto per PCB con chip di grandi dimensioni come i BGA e altri in cui alcune connessioni sono invisibili anche quando si utilizza il metodo ottico.